Vacuum Gauges
7 products
Showing 1 - 7 of 7 products
Vacuum Gauges Australia – Precision Testing for Optimal Performance
The vacuum gauge provides an easy and efficient way to test the vacuum level of vacuum pumps, vacuum lines, and chambers. Designed for accurate measurements, these gauges ensure optimal performance and reliability in various applications.
For professionals and technicians in Australia, having a high-quality vacuum gauge is essential for maintaining system efficiency and troubleshooting potential issues.
Check our top brands such as Mastercool, Javac, Robinair, Fieldpiece, Imperial, Hydrocell, Yellow Jacket, Inficon, Neutronics, and many more to easily find the right tools you need.
HOW TO USE A VACUUM GAUGE
Are you interested in a better vacuum? Start by learning how to use your high quality vacuum gauge correctly.
Any HVACR technician has to have a digital vacuum gauge. You can use it to read the difference in atmospheric pressure between the air conditioning unit's interior and exterior. You can use this to identify problems with the pressure inside the unit. Usually, this is the initial stage of a service you offer. We at HVAC Shop wish to aid in the job readiness of any HVACR technician. Continue reading to find out more if you have more queries regarding how a vacuum gauge works and how to read one.
What is a Vacuum?
Space is frequently mentioned when the subject of vacuum is raised. Any air pressure less than the atmospheric pressure normally found on Earth is said to be in a vacuum. The atmospheric pressure on Earth is approximately 14.7 pounds per square inch (psi). Although there is a vacuum in length, it is not perfect.
A complete vacuum is a region from which all matter has been eliminated. It is not feasible to duplicate this on Earth as we know it. The harder and more costly it is to make, the closer you attempt to go to a perfect vacuum.
Measurements of the relative vacuum may need to be more consistent or effective depending on several circumstances. These include variables like varying weather or altitudes, both of which have an impact on how much atmospheric pressure the Earth produces.
Why Pull Vacuums?
It's crucial to get rid of all moisture and non-condensable gases before introducing any refrigerant while installing a new HVAC tools or doing repairs. Other non-condensables, such as nitrogen, air, water, or other refrigerants, might affect the system's pressure readings and cause moisture to convert to acid and freeze. The predicted life and effectiveness of the system can be directly increased by getting rid of all of these. That's how easy it is.
500 Microns
Every moisture and non-condensable gas must be boiled off and removed from a system using a deep vacuum of 500 microns or less. Despite how tiny the microns are, there is a significant difference between 500 and 1,000 microns. Water boils at one degree Fahrenheit at 1,000 microns. Water boils at -12 degrees Fahrenheit at 500 microns. Ensure the vacuum you pull is strong enough to eliminate all moisture and non-condensable gases, and ensure the system is ready for the refrigerant.
Although the industry standard for vacuum pressure is 500 microns, you should always check the handbook before pulling one because every system maker has their own.
Because a micron is so tiny, readings on vacuum gauges frequently fluctuate. Even jolting a fitting or bumping a meter can cause the discrepancies we are detecting to vary. You should better understand what fluctuations in your vacuum gauge readings can signify.
HOW TO READ A VACUUM GAUGE
Setting it Up
- Use the Right Tools
A vacuum gauge is the best instrument for measuring deep vacuum and "seeing" what is happening with the system. While a rapid micron rise suggests a system leak, a slow micron rise shows moisture still burning off. For convenience, digital manifolds may include an accurate vacuum gauge, but faulty hoses, connections, and distance from the system can impact readings.
- Microns
Put the vacuum gauge on the system where you would like the 500 microns to be! The vacuum gauge should be positioned as far back on the system as possible because this is the last location to reach 500 microns because of parts of the system and line set bends that cause limitations. If you want to get the technique down to 500 microns more quickly, don't position it directly next to the pump producing 20 microns of absolute vacuum. Similarly, installing a thermostat now above a register is not a good idea.
- Clear Restrictions
Any flow constraints in the system that could hinder the vacuum pump's ability to pull the system into a deep vacuum must be removed. It would be best if you had the shortest hose size and the largest hose diameter to pull the vacuum the fastest. Occasionally, connecting the pump with a pair of charging hoses might be simpler. Still, vacuum-rated hoses have a bigger diameter, and that extra space allows for greater flow to pull a vacuum. Pull the valve cores from the system's service ports as well. Each of them results in a restriction that lengthens the time it takes for your evacuation.
Vacuum Gauge Reading

- Normal
This reading of between 17 and 22 inches of mercury is typical. Remember that this figure is optimum for engines running at sea level with factory cams. Readings may be a little bit lower at higher elevations. For every 1,000 feet above sea level, the reading should be roughly one inch lower. Additionally, for cams with greater aggression, you should anticipate lower readings.
- Consistent or Extreme Low Reading
The gauge on the left displays a very low level that remains stable over time. It indicates that the engine is creating less suction and less power. Blowing because of worn piston rings and possible valve timing or late ignition are common causes of steadily low readings. An incredibly low number could also result from an air leak at the throttle body or intake manifold.
- Steady Low/High Swing
A steady swing between high and low readings typically indicates a blown head gasket connecting two adjacent cylinders. You'll need to do a compression test to be sure.
- Idle Rapid Vibration
If the needle rattles fast between 14 and 20 inches of mercury but stops as the rpm increases, you may have worn valve guides. The rate at which the needle vibrates could be used to count the number of worn valve guides.
- Fluctuation Under Acceleration
On the other hand, if the needle on the gauge moves around when the engine revs up, the valve springs are likely too frail. The gauge's swing ranges from 10 to 22 inches of mercury, depending on the engine's speed.
- Needle Drop
The vacuum gauge frequently starts out in the normal range when there's an exhaust limitation but quickly lowers when the rpm is increased. Most likely, one or more exhaust system components are restricted or damaged.
- Abnormal High Reading
In contrast, a clogged or little air cleaner could cause a reading greater than usual, depending on how hard the engine draws in air.
- Normal/Low Trend
If the needle repeatedly dips to a low number, rises to normal, and then repeats the pattern, you're probably looking at a burnt, jammed, or leaky valve. A blocked valve frequently causes more random decreases in this pattern.
How to Understand Vacuum Readings
- Fluctuations are Normal
After each vacuum pull, the system requires time to equalise to a stable pressure. Throughout the process, your values may change; occasionally, these modifications may be unexpected and lead you to suspect a leak. However, it is normal for these varied values to exist. Wait five minutes after pulling down to 500 microns to give the system time to stabilise. Even after you take out the vacuum, the levels will change. Numerous things could be at blame for this.
- Ball-Valve
First, you should be aware that the hose ball valve you use to connect your vacuum pump frequently contains little gas. This minuscule amount of gas in the valve can cause your readings to rise immediately as you close the valve because vacuum gauges monitor tiny quantities of micron change. If you turn this valve and see a small increase in pressure followed by a swift drop in force, this is typical and not cause for alarm. During the evacuation, frequently open and close the ball valve to avoid this.
- Outgas
Outgassing may also be a contributing factor in the variations. When you pull a vacuum, every hose and O-ring in the system may move slightly, which may cause a small amount of gas to be released. Much like the ball valve we stated earlier, some gas could be retained in valves or fittings. Only when there's a nearly absolute vacuum will they discharge this gas. The readings could sporadically change as a result of this. It's typical once more.
- Too Much Moisture
The vacuum pump has its limitations. If pulling a vacuum takes much longer, there may be too many pollutants or moisture in the system that must be cleaned out. A triple evacuation is a smart approach to ensure your system is free of extra moisture. It entails lowering the vacuum to between 1,000 and 2,000 microns, flushing nitrogen into the system for five minutes at a pressure of 3 to 5 PSIG, and then lowering the vacuum to 500 microns once more. A third time through the procedure, the vacuum should be reduced to 300 microns, followed by another nitrogen flush and a ten-minute standing vacuum test with the pump disconnected.
- Leak
Close the valves, separate the system, and switch off the pump once you've reduced your approach to 500 microns. To determine whether the system can maintain pressure and whether the vacuum you pulled was deep enough. The microns will fluctuate somewhat as the system reaches equilibrium. How can you determine the difference between the modest changes in pressure due to outgassing or other typical fluctuations and those that are genuinely caused by a leak?
If the micron reading rapidly rises and continues until it hits atmospheric pressure after you've isolated the pump, you likely leak.
If the pressure gradually rises with time and eventually plateaus at a thickness greater than 1000 microns. It indicates that you have some water in the system. You must turn the pump on again and pull a deeper vacuum.
As a result, it is essential to isolate the system and attach your vacuum gauge directly to it. By doing this, you can make sure that any potential leaks in your vacuum system's hoses or connections have no impact on the reading of the vacuum gauge.
WHERE TO CONNECT THE VACUUM GAUGE
Understanding the Basics
Nothing is more fundamental than the reality that an engine is only a large air pump. Establishing a low-pressure zone between the intake manifold and cylinders pulls air in, compresses it, adds some gasoline, starts a fire, produces heat and pressure, and then pumps out the used exhaust. Today's obsession with everything technological can cause us to ignore traditional mechanical problem symptoms and the automatic diagnostic tools used to diagnose them. Vacuum gauges are commonly in this category, yet the insight that a vacuum gauge may provide is as important today as it was 30, 40, or 50 years ago.
Keep in mind that engine vacuum is ambient pressure less. The intake manifold serves as the starting point for measuring engine vacuum. A manifold vacuum is measured by attaching a gauge to an intake tap. Be aware that the vacuum will change depending on where in the engine you are, like just at the intake and exhaust ports or above or below the throttle valve.
Ported vacuum is air drawn through a hole in front of the throttle. In contrast to how it affects manifold vacuum, throttle opening influences ported vacuum. For instance, manifold vacuum is at its highest level at closed throttle. However, when the throttle is closed, there is little to no suction at a port in front of the throttle plate. Such a port only experiences a vacuum when the throttle opens.
It's crucial to remember that under all engine running circumstances, a manifold vacuum is used to fuel vehicle systems that require a consistent supply of low-pressure air. These systems are power brake boosters, air conditioning vacuum motors, and emissions controls.
Connecting the Vacuum Gauge
When making a DIY diagnosis, keeping an eye on your high-horsepower engine, or trying to hyper-mile, monitoring the engine vacuum is helpful information. Splicing into the proper vacuum line is essential to receiving the right readings, whether using a gauge you are installing in your car or just using an indicator under the hood.
- Find the ported engine vacuum while the engine is running and the brake pedal is engaged. Locate a vacuum hose fastened to the intake manifold and carefully remove it. You've discovered a reliable vacuum source if the engine idling changes and the hose starts to hiss.
- Stop the car's engine. After removing the original vacuum hose, install two inches of vacuum pipe onto the port. Place the vacuum "T" between the vacuum line's two ends. You can now attach your vacuum gauge to the T-fitting and conduct your tests if you use one.
- If you're mounting a vacuum gauge inside the car, follow the manufacturer's instructions. If the metre needs suction, run a vacuum line from the T-fitting into the car. The vacuum line should be carefully inserted through the rubber gasket where the wiring harness hits the firewall, and then it should be directed to the gauge. Install the MAP sensor as the manufacturer instructs and run the sensor wire into the car as if the gauge needs an electrical reading from the sensor.
Do It Right
It is always more cost-effective to complete a task thoroughly than hastily along with damaging consumer confidence, having to send a service specialist back for a warranty repair results in a triple loss of income for the contractor.
Because the follow-up service call isn't reimbursable, the first loss occurs. The expense of replacing the equipment malfunctioning due to incorrect installation constitutes the second loss. The technician's absence from lucrative calls during this period accounts for the third loss.
In conclusion, an electronic vacuum gauge is the only device confirming that a system has been adequately evacuated before refilling with refrigerant. And one of the best methods to safeguard your revenues from unnecessary warranty repairs is a complete evacuation.



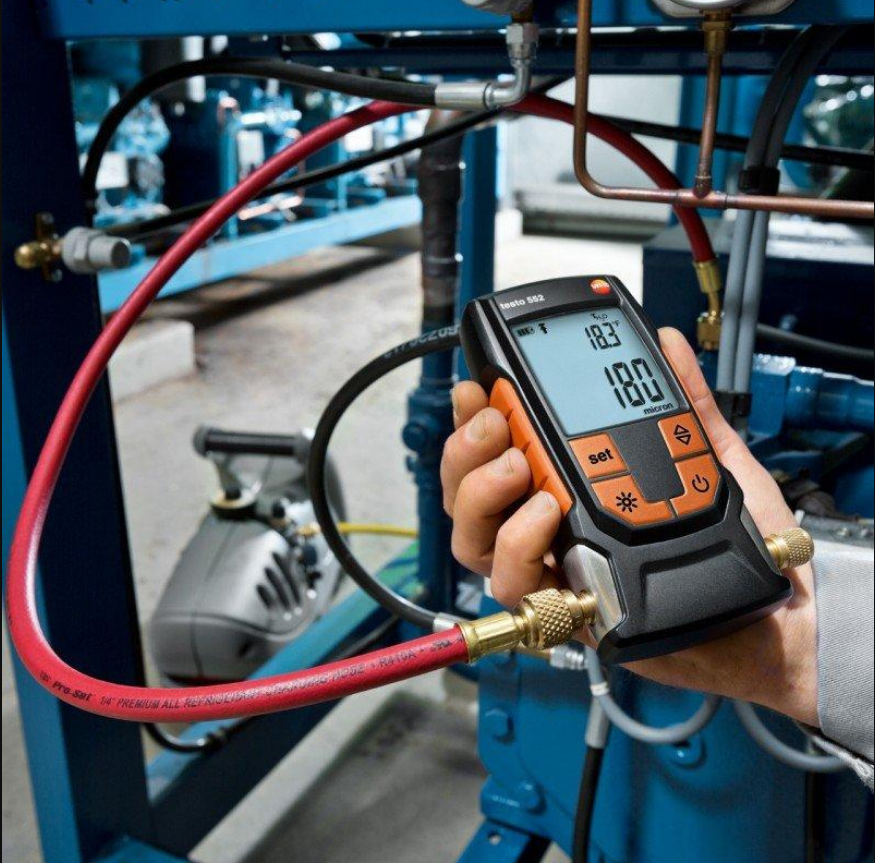


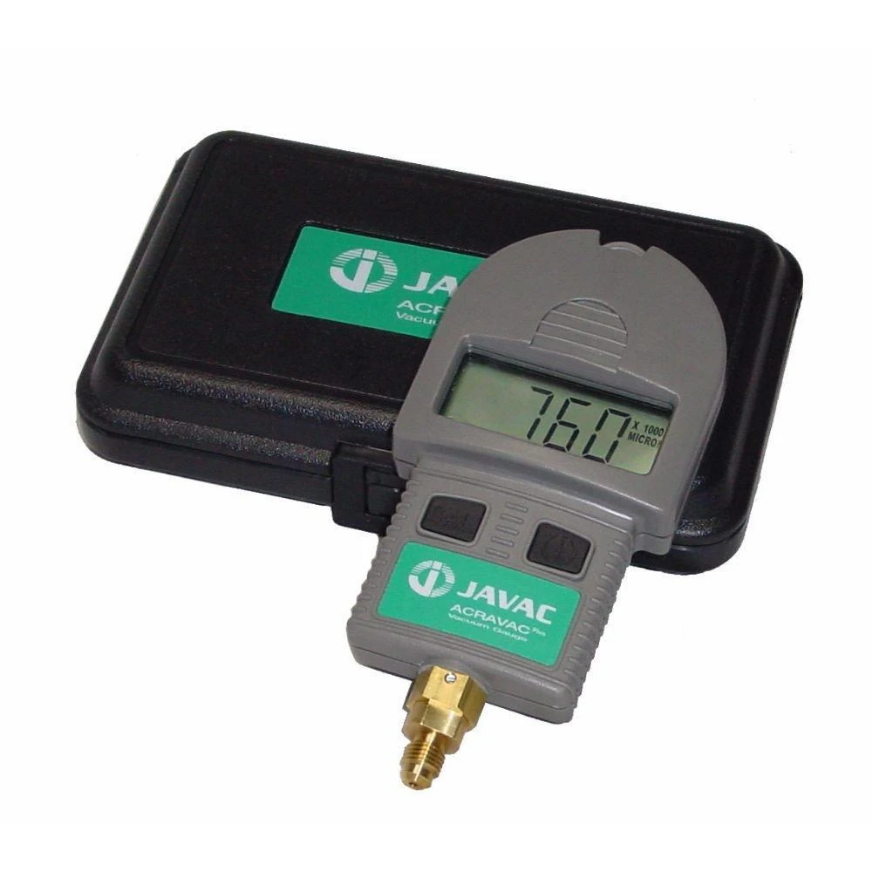
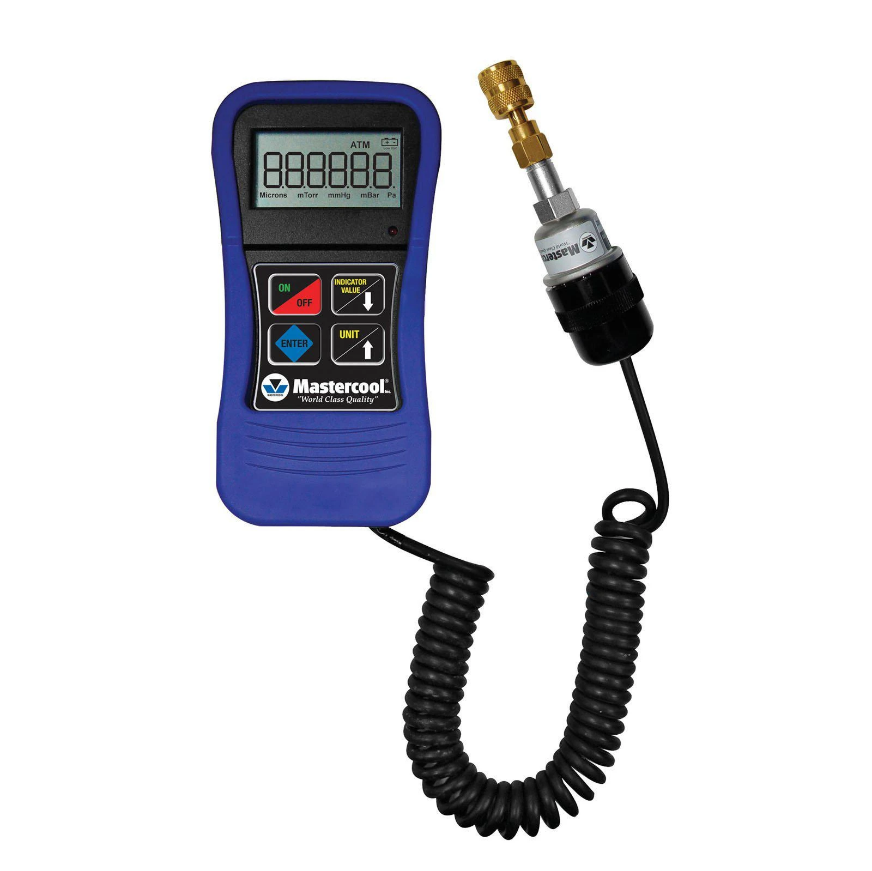
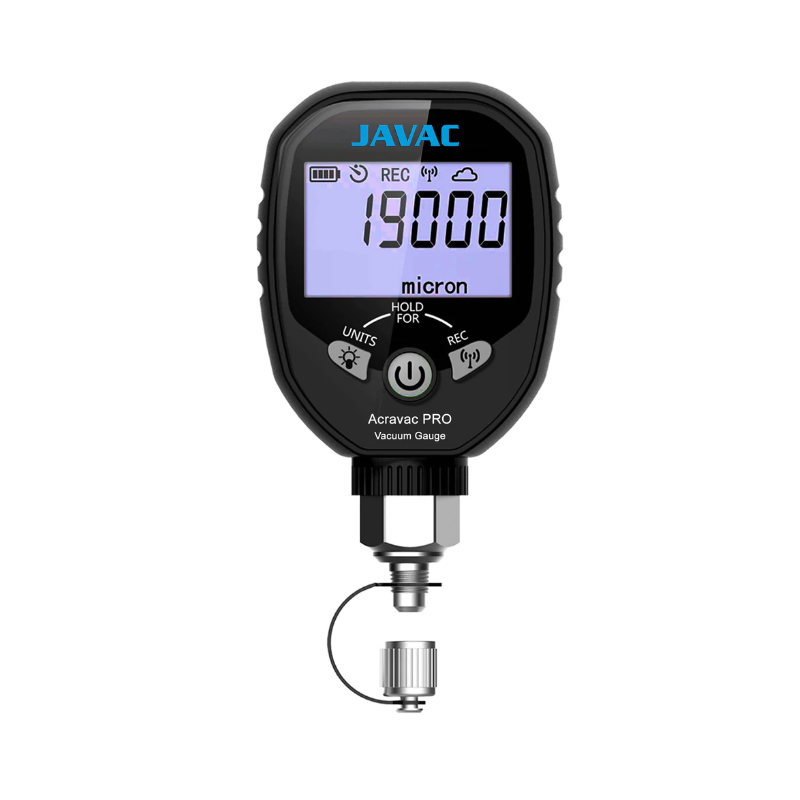

